- Como parte del proyecto DOMMINIO de la Unión Europea, el Instituto IMDEA Materiales está ayudando a crear sensores inteligentes integrados que proporcionarán a los ingenieros en tierra información actualizada en tiempo real sobre las aeronaves durante el vuelo.
- Estos sensores se instalarán por 3D y se incorporarán a los componentes clave de las aeronaves durante su fabricación, lo que supondrá un importante ahorro de costes y tiempo para las compañías.
El Instituto IMDEA Materiales está desempeñando un papel fundamental en el desarrollo de la tecnología de sensores de aviación de próxima generación, que permitirá la supervisión en tiempo real de los componentes del fuselaje en vuelo.
Estos sensores inteligentes, diseñados para ser integrados en las propias piezas, podrían proporcionar enormes beneficios tanto en coste como en seguridad a la industria aérea en los próximos años.
Éste es, al menos, uno de los objetivos del proyecto DOMMINIO (Digital Method for Improved Manufacturing of Next-Generation Multifunctional Airframe Parts), financiado por la Unión Europea.
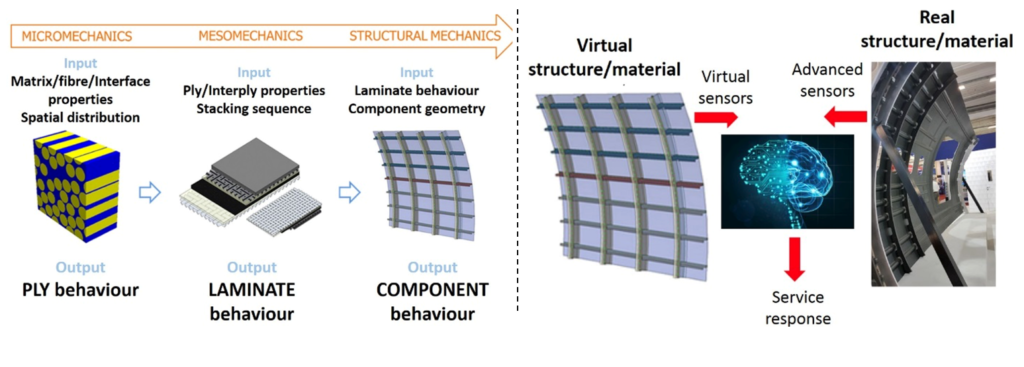
El papel de IMDEA Materiales dentro de este consorcio de investigación internacional consiste en llevar a cabo el trabajo experimental y de simulación avanzada necesario para desarrollar la tecnología de sensores, y en la creación de modelos virtuales de alta fidelidad denominados «gemelos digitales».
«Se llaman gemelos digitales porque son modelos digitales muy precisos que se actualizan durante todo el ciclo de vida, replicando la pieza o componente físico de la aeronave en tiempo real», explica el investigador de IMDEA Materiales Moisés Zarzoso.
«Con esa información, las simulaciones que estamos desarrollando podrán analizar el riesgo que un potencial impacto pueda inducir en la integridad estructural del componente y determinar su vida útil restante».
Esta investigación se lleva a cabo a través del grupo de Materiales Compuestos Estructurales del Instituto, dirigido por el Profesor Carlos González. El papel de simulación y modelización en el desarrollo de estos sensores de vanguardia permite a los investigadores superar unos límites de la caracterización de materiales.
«Para diseñar el sensor, tenemos que ser capaces de caracterizarlo», dijo Zarzoso. «Podemos hacerlo mediante experimentos, pero también con simulaciones.
«Con las simulaciones se puede ir más allá en algunos aspectos. Se pueden estudiar los efectos de ciertos parámetros de diseño que serían imposibles, o extremadamente caros, de probar experimentalmente».
La tecnología que se está desarrollando en el proyecto DOMMINIO no sólo permitiría el control en tiempo real, sino que además también aplicaría técnicas avanzadas de impresión en 3D y avances en la producción de fibras de nanotubos de carbono (CNTs) para integrar el sensor dentro de la pieza durante su fabricación.
Esto significa que ya no sería necesario fijarlos después de la producción del componente, permitiendo además una reducción significativa de la cantidad de cableado eléctrico necesario para alimentar la actual generación de sensores de las aeronaves.
La combinación de sensores más ligeros y eficientes, junto con la reducción del cableado, hará que los aviones sean más eficientes desde el punto de vista del consumo de combustible y, por tanto, más respetuosos con el medio ambiente y más económicos para sus operadores.
El grupo de Nanocompuestos Multifuncionales, dirigido por el Dr. Juan José Vilatela, también participa en el proyecto DOMMINIO y ha asumido el papel de desarrollar el sensor de CNTs y el análisis experimental de sus propiedades piezoresistivas cuando se integran en el componente.
«Los sensores se están desarrollando para ser fabricados con estas fibras, que son increíblemente ligeros en comparación con los materiales existentes y que además consumen muy poca energía», explicó Zarzoso.
«También son imprimibles en 3D y, dado que son fibras de CNTs, pueden integrarse fácilmente en un componente fabricado con fibra de carbono tradicional, que es un material muy común en la producción de aviones».
Los beneficios de esta tecnología, sin embargo, van más allá de la reducción de peso. También permitirá a las aerolíneas adoptar programas de mantenimiento más eficientes y eficaces.
«El mantenimiento de los aviones está programado, después de una cantidad predeterminada de horas de vuelo, hay que dejar de volar el avión para revisar las distintas piezas y componentes», dijo Zarzoso.
«Si se pudiera tener una nueva forma de diseñar y fabricar estos aviones, que pudiera dar información en tiempo real de los sensores sobre la salud estructural del fuselaje, se podría mejorar el proceso de mantenimiento”.
«Esto supondría un importante ahorro de tiempo y costes para las aerolíneas al mismo tiempo que se mantienen los exigentes estándares de seguridad de las aeronaves».
El proyecto DOMMINIO está financiado por la Unión Europea a través del programa de investigación e innovación Horizonte 2020.
Junto con el Instituto IMDEA Materiales, colaboran en el proyecto el coordinador el Centro Tecnológico AIMEN de Galicia (Cordinador), el gigante aeroespacial británico BAE Systems, la empresa aeronáutica española ACITURRI, la Universidad Técnica Nacional de Atenas, la escuela de ingeniería Arts et Métiers ParisTech, y el Centro Industrial de Plásticos y Composites (IPC) con sede en Francia.
También forman parte del consorcio el Instituto Nacional de Investigación Aeroespacial «Elie Carafoli» en Rumanía, Tortech nano-Fibers LTD, DASEL Systems, la consultora Innovation in Research & Engineering Solutions (IRES), ESI Group y la Red Europea de Ciencias Aeronáuticas (EASN).
You can find out more about the DOMMINIO project here: https://domminioproject.eu/