- Como miembro del proyecto europeo HIPped Ultrafan IPT Casing (HUC), gestionado por el fabricante de motores y turbinas español ITP Aero, IMDEA Materiales colaboró en el desarrollo de la carcasa de la turbina de presión intermedia (IPT) del UltraFan.
- El demostrador del motor UltraFan® es la base de una futura familia de motores un 25% más eficiente que la primera generación de motores Trent. Los primeros ensayos del demostrador UltraFan se llevarán a cabo este año utilizando combustible de aviación 100% sostenible.
El Instituto IMDEA Materiales ha desempeñado un papel importante en el desarrollo del prototipo del motor UltraFan® de próxima generación de Rolls-Royce.
A principios de este año, ITP Aero, una de las empresas de motores aeronáuticas más grande del mundo, hizo entrega de la primera turbina de presión intermedia (IPT por sus siglas en inglés) para el motor UltraFan® de Rolls-Royce.
Las primeras pruebas se realizarán a lo largo de este año con combustible de aviación 100% sostenible (SAF por sus siglas en inglés).
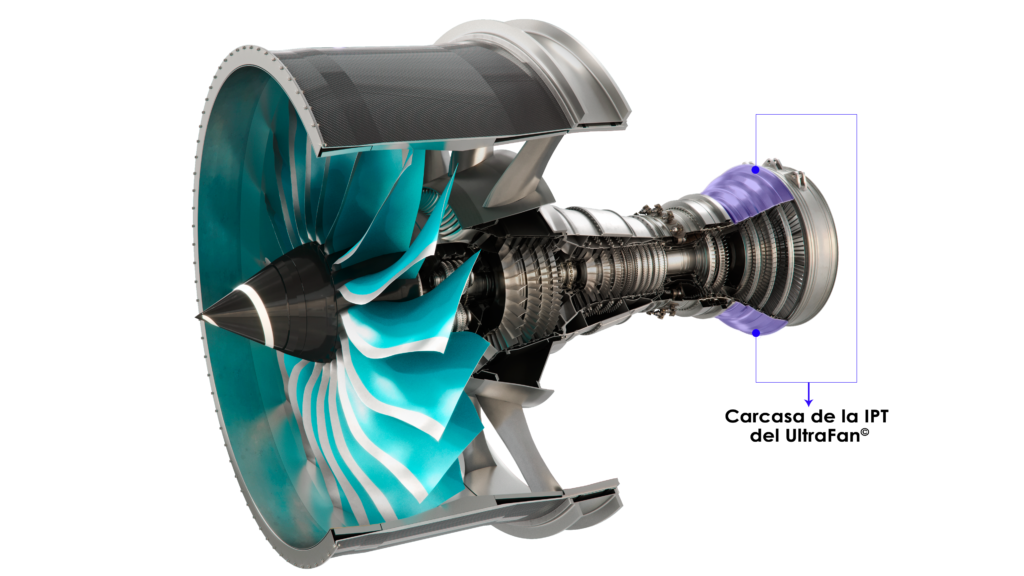
En el marco del proyecto HIPped Ultrafan IPT Casing (HUC), IMDEA Materiales colaboró en el diseño y las pruebas de la carcasa de la turbina de presión intermedia (IPT) del UltraFan.
La carcasa es el principal componente estático de la IPT del UltraFan; es el soporte de los vanos y del resto de piezas estáticas, y soporta la transmisión de cargas con el resto del motor.
Adicionalmente, protege la aeronave, conteniendo los álabes de la turbina en caso de fallo. La IPT es un módulo clave del futuro UltraFan, diseñada para funcionar a velocidades muy altas que permiten optimizar el consumo de combustible y emisiones de CO2 del motor.
Uno de los investigadores principales de IMDEA Materiales en el proyecto, Juan de Pablos Gómez, destacó cómo la tecnología desarrollada a través del proyecto HUC dará lugar a considerables beneficios para la industria de la aviación.
«Este motor UltraFan es un demostrador de una serie de tecnologías que permitirán recortar el consumo de combustible en un 25% y reducir los niveles de ruido en un 35% en las próximas décadas», explicó de Pablos, cuyo trabajo en el proyecto HUC fue el componente central de su tesis doctoral recientemente defendida.
«Otros motores de tipo turbofan que entren en funcionamiento en la industria de la aviación comercial podrán aprovechar estas tecnologías para reducir las emisiones y también los costes de fabricación del propio motor».
El papel de IMDEA Materiales se centró en su grupo de investigación de Mecánica Computacional del Sólido, dirigido por el Profesor Ignacio Romero, y en el grupo de Simulación Física, dirigido por el Dr. Ilchat Sabirov.
«[Nosotros] participamos principalmente en la componente de simulación computacional, abordando el comportamiento mecánico de esta nueva carcasa que está hecha de una nueva superaleación», dijo de Pablos.
«Como el motor UltraFan se basa en ciclos termodinámicos más eficientes, tendrá que ser capaz de soportar temperaturas más altas. Nuestra misión, mediante el uso de una nueva tecnología desarrollada en la investigación computacional, era poder evaluar estas propiedades mecánicas del material antes de que se sometiera al proceso de certificación requerido.
«También era muy importante para nosotros comprender el comportamiento de este material en condiciones extremas de tensión y velocidad de deformación, como cuando se somete a un posible impacto de los álabes».
La carcasa en cuestión alberga los álabes de la turbina y conecta la IPT con el resto del motor. Como tal, no sólo debe ser resistente al calor, sino también lo suficientemente fuerte como para contener las piezas del motor y evitar que salgan despedidas y golpeen el fuselaje del avión en caso de daños internos del motor.
El carácter pionero del proyecto HUC se basa en el uso innovador de la tecnología de prensado isostático en caliente (HIP) y de la superaleación en polvo Astroloy. Según ITP Aero, el Astroloy ofrece un mejor rendimiento mecánico a altas temperaturas en comparación con las superaleaciones más utilizadas.
En la actual generación de motores, estas carcasas se fabrican normalmente con la superaleación de níquel Inconel 718, un material muy utilizado en diversos componentes de la industria de los motores de aviación.
IMDEA Materiales pudo aportar al proyecto su experiencia tanto en simulación como en trabajo experimental. Además de las contribuciones computacionales del Instituto, el grupo del Dr. Sabirov también realizó una exhaustiva caracterización mecánica y microestructural de las muestras de Astroloy.
“De este modo, se estudió una amplia gama de propiedades mecánicas relacionadas con su aplicación para garantizar la alta calidad del componente final,” dijo el Dr. Sabirov.
El Instituto madrileño fue uno de los miembros de un consorcio internacional dedicado al diseño y la fabricación de la nueva carcasa que fue coordinado por el Centro Vasco de Estudios e Investigaciones Técnicas (CEIT) bajo la dirección de ITP Aero.
También participaron el Consorcio Nacional Interuniversitario de Ciencia y Tecnología de los Materiales (INSTM) de Italia, la Universidad del País Vasco y el fabricante de polvos Aubert & Duval SAS.
El proyecto HUC fue financiado conjuntamente por la Unión Europea y las empresas aeronáuticas europeas a través del programa Clean Sky 2. El informe final del proyecto fue aprobado recientemente por la Comisión Europea.
Puedes leer mas sobre el proyecto HUC aqui: http://huc-cs2.eu/