- Los investigadores del Instituto IMDEA Materiales han desarrollado un recubrimiento resistente al fuego aplicable a los paneles de aluminio habitualmente utilizados en carcasas y cajas protectoras de baterías.
- El recubrimiento ha demostrado proteger los paneles de la penetración térmica a temperaturas de hasta 1400℃.
Los investigadores del Instituto IMDEA Materiales han presentado un innovador recubrimiento retardante de llama, efectivo con grosores de tan solo 350 micrones, que mejora drásticamente la resistencia al fuego de las carcasas de baterías utilizadas en vehículos eléctricos y aeroespaciales.
Este avance promete reducir los riesgos asociados con fenómenos como el descontrol térmico en baterías de ion litio, al mismo tiempo que mejora la aplicabilidad y el rendimiento de las baterías en escenarios de alta temperatura.
Los hallazgos son el resultado del trabajo de los investigadores de IMDEA Materiales, Wei Tang y Yunhuan Liu, ambos miembros del grupo de Polímeros de Alto Rendimiento y Retardantes de Fuego del instituto, bajo la dirección del Prof. Dr. De-Yi Wang.
En su investigación, los científicos realizaron pruebas de penetración de fuego tanto en placas de aluminio de 3 mm recubiertas como no recubiertas, a temperaturas de hasta 1400°C.
Este tipo de prueba es de gran importancia en diversas industrias, ya que permite a los investigadores determinar cuánto tiempo tarda el fuego en penetrar un material, lo que indica su susceptibilidad a fallas estructurales y peligros potenciales.
«Encontramos en las pruebas que los sustratos de aluminio sin recubrimiento duraban apenas 135 segundos antes de sucumbir a la penetración térmica a temperaturas extremas», reveló Tang.
«Sin embargo, los mismos sustratos con un recubrimiento de apenas 350 micrones mostraron una resistencia al fuego notable, manteniendo su integridad estructural incluso después de 15 minutos de exposición a altas temperaturas. Las pruebas también mostraron que la temperatura posterior de la placa no superó los 450℃», agregó.
Esto está muy por debajo del punto de fusión del aluminio, que es de aproximadamente 660℃. Si bien las carcasas de baterías normalmente no están expuestos a tales temperaturas extremas en condiciones de operación normales, esto puede suceder en ciertas situaciones, especialmente en aplicaciones aeroespaciales o en procesos industriales.
Sin revelar la composición exacta del recubrimiento, los investigadores detrás del avance lo describieron como un «recubrimiento nanotecnológico retardante de fuego basado en polímeros funcionales».
Además del aluminio, se ha demostrado que el recubrimiento también es efectivo cuando se aplica a otros materiales, como espumas de polímero, compuestos reforzados con fibra, y acero, entre otros.
El secreto de su eficacia radica en el hecho de que, cuando se expone a una llama directa, el recubrimiento se convierte de inmediato en una barrera en la superficie del material.
La composición de la capa de barrera está diseñada para permanecer estable a altas temperaturas y sirve como barrera protectora y aislante del sustrato subyacente frente al calor directo de la llama.
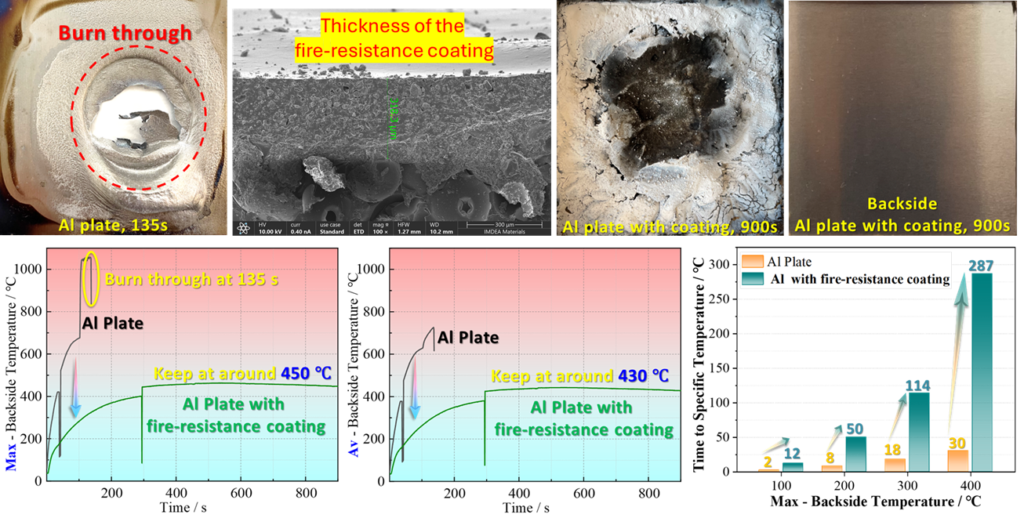
Además de sus propiedades mejoradas de retardante de fuego, el pequeño grosor del recubrimiento requerido, de apenas 0.35 mm, también lo hace más rentable y eficiente para aplicaciones industriales.
«Sin embargo, aunque sabemos que el recubrimiento es efectivo una vez aplicado, todavía hay trabajo por delante en mejorar su procesabilidad», reconoció Liu.
«En este momento, este recubrimiento debe aplicarse manualmente para lograr una dispersión y un grosor adecuados en la superficie del material. Sin embargo, estamos en el proceso de optimizar su procesabilidad para la fabricación industrial».
«Además, la producción del recubrimiento en sí es bastante simple y económica, lo que lo hace atractivo en cuanto a la posibilidad de su desarrollo a una escala industrial».