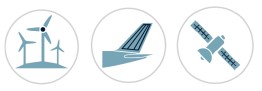
Titanium aluminum nitrides (TiAlN) are currently the most versatile coatings in terms of performance with various applications in industry: as wear-resistant coatings for cutting tools; for increasing productivity in die casting, reducing soldering and retarding fire cracks; for plastic processing, such as injection molding and extrusion; for metal forming, like blanking, deep drawing, punching or trimming; and they are also finding applications for protecting pieces from high abrasion, like turbine blades.
The industry-standard technique for the deposition of these coatings is cathodic arc deposition, although it is well known for producing porous, rough coatings with a high number of defects and particulates. Moreover, these coating typically offer a high hardness, but a limited fracture toughness, leading to relatively brittle coatings, than tend to crack along the existing defects, such as the boundaries of their columnar grains.
The ever-increasing demands from industry and technology call for better performing materials. IMDEA Materials Institute is working in different directions to produce new coatings for extreme conditions that combine, not only a high hardness, but also a large fracture toughness. Several directions are followed for this:
- The exploitation of novel techniques like High-Power Impulse Magnetron Sputtering (HiPIMS), which has the potential to vastly reduce the downsides of Arc Evaporation by the application of high-energy ion bombardment over the coating surface, resulting in much denser defect-less coatings.
- The development of quaternary TiAlN coatings by the addition of other elements such as Cr, Si, Zr, B, Ni or others or the use of nanolaminated structures. In particular, a better understanding of the microstructure formation is seek with the objective of suppressing columnar growth, which is known to compromise the fracture toughness of the coatings. For instance, Fig. 1 show an example on how the addition of small amounts of Ni into a TiN coating suppresses columnar growth, which has strong implications on the coating fracture resistance.
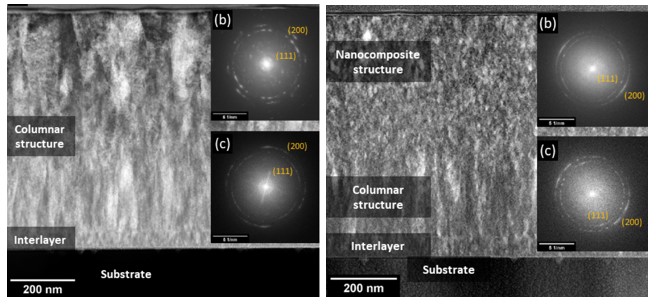
- The exploitation of novel advanced characterization techniques. Nowadays, the mechanical properties of coatings are characterized by conventional nanoindentation tests. However, IMDEA Materials is expert on the application of novel nanomechanical tests in coatings, such as high temperature nanoindentation for the determination of hardness at elevated temperature, the micropillar splitting test (Fig. 2) for the determination of fracture toughness or the incremental Focused Ion Beam (FIB) milling technique for the determination of residual stresses. These techniques provide valuable fundamental information for the development of new coatings for extreme environments that cannot be obtained by conventional testing approaches.
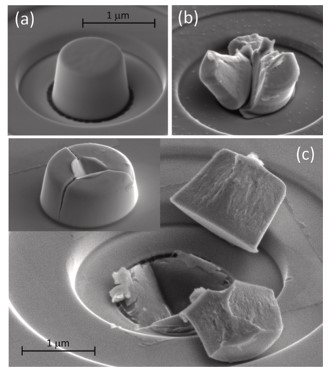