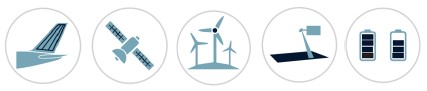
Current trends to reduce weight, energy consumption and improve functionality are leading to new materials with complex microstructures, whose behavior can only be understood from the synergetic contribution of processes occurring at multiple length scales (from nm to m). Examples of these materials are structural composites, duplex alloys or materials with evolving microstructures that deform by unconventional deformation mechanisms (TWIP and TRIP steels), nanoporous foams or hierarchical meta-materials produced by Additive Manufacturing. The design of new materials and their application requires a complete fundamental understanding of their behavior and in situ studies are crucial to achieve this.
The IMDEA Materials Institute gathers experts in advanced characterization that make use of state-of-the-art in situ devices (both commercial and developed in-house) to test materials under different loading configurations (tension/compression/fatigue at ambient and elevated temperature) and to physically simulate processing (e.g. solidification or resin infiltration of fiber preforms). Tests are carried out on specimens ranging in size from hundreds of nanometers to several millimeters under different characterization beams, such as Scanning Electron Microscopy (SEM), Focused Ion Beam (FIB), Transmission Electron Microscopy (TEM), as well as X-ray Computed Tomography (XCT) and X-ray diffraction (XRD), both using laboratory and synchrotron X-ray radiation (http://www.materials.imdea.org/scientific-infrastructure). Some examples of the offered capabilities are:
- In situ mechanical testing in the SEM and TEM at different scales (macro-micro-nano)
In situ mechanical testing in the SEM and TEM, as shown in Fig. 1, can provide information on deformation mechanisms and damage evolution in advanced metallic alloys and structural composites. This allows detecting “hot spots” in the material microstructure that can lead to damage accumulation and the final failure of engineering components. This fundamental knowledge can be used to tailor better microstructures through the control of the processing methods and to produce longer lasting products.
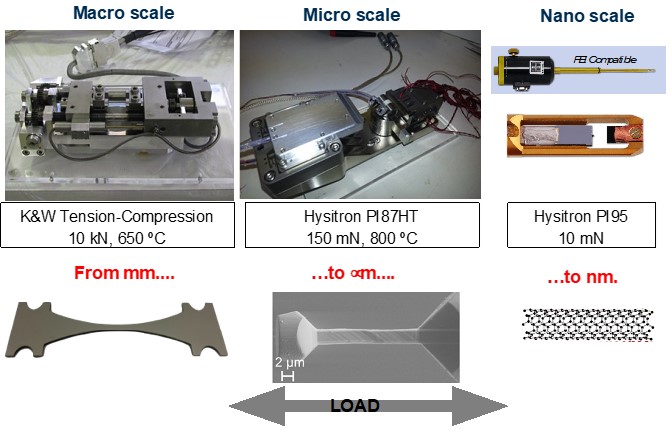
- In situ XCT devices for processing and mechanical characterization
Many industrial processes of engineering materials are not yet fully understood. This is also true for the mechanical behavior of many materials. One way to shed some light on the effect of the parameters affecting the processes, or the effect of the microstructure on the mechanical properties is to be able to look into the materials as the process or the mechanical deformation is occurring. This requires the use of non-destructive techniques as e.g. XCT combined with appropriate devices able to replicate the desired event. Examples of developed devices at IMDEA Materials for process replication during XCT are: a) for composite materials: devices for resin infiltration into fibers (infusion and VARTM), curing device for autoclave and out-of-autoclave processes, b) for metals and alloys: resistive furnaces for studies of directional solidification or phase formation and chemical reaction by infiltration of liquid metals into porous preform, portable induction furnaces for in-situ XCT and XRD heat treatments. For mechanical testing of many materials during XCT inspection, a tensile/compression/low cycle fatigue with a temperature module of up to 600ºC has been also developed at IMDEA.
Fiber-reinforced polymers are extensively used in the automotive, aerospace and energy industries for structural applications. The interest in Liquid Composite Molding (LCM) processes, for the production of composite materials has grown in the last years, especially in the Vacuum Assisted Resin Transfer Molding (VARTM) process due to its relative low cost and the possibility to process large panels, such as wind turbine blades. However, the large amount of physical variables that control the infusion process impacts on the quality of the panels and the physical process is not well understood. Therefore, an in situ infiltration device was developed at IMDEA Materials Institute (Fig. 2) to investigate the infusion process by XCT. The fundamental understanding obtained was key to improve the VARTM process.
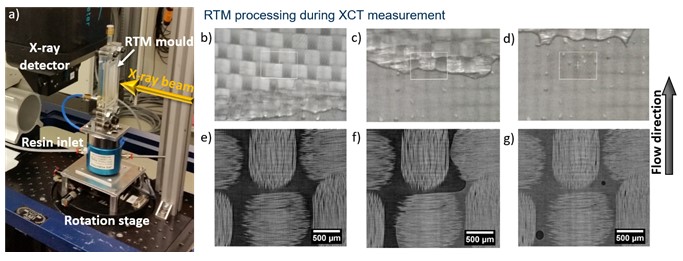