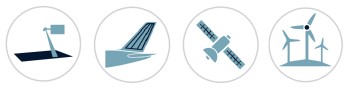
IMDEA Materials offers a mature, fully stand-alone technology able to predict the mechanical response of an engineering alloy as function of its microstructure [1]. This technology is able to provide the anisotropic elastic properties and stress-strain elastoplastic curves, the creep response and fatigue life estimation. The inputs are grain size distribution, texture (EBSD map or ODF) and alloy characteristics (lattice type, critical resolved shear stress, or some macroscopic experimental data for fitting). The technique can be applied to metals fabricated via Additive Manufacturing (AM) or conventional casting and solid state processing. This technology is based on computational homogenization of polycrystals in which the mechanical macroscopic response of the material is obtained by the simulation of a Representative Volume Element (RVE) of the metal microstructure. The RVE contains a representative sample of grains, which fulfills the experimentally measured grain size, shape and orientation (see Fig. 1).
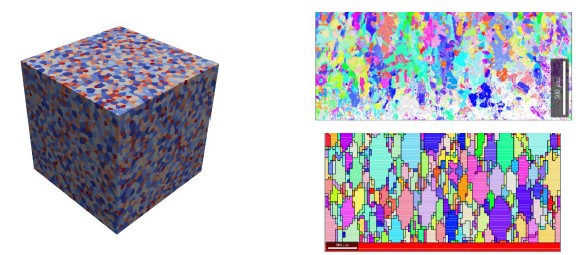
The simulation of the mechanical response of the RVE is performed by Finite Elements or using a home-made fast and robust simulation solver based on the fast Fourier transform, FFTMAD. The grain response is based on the crystal plasticity model and is introduced by a UMAT user-subroutine, valid both for Finite Elements (ABAQUS) and FFTMAD. A large library of crystal subroutines have been developed: phenomenological models to be fitted with macroscopic tests, physically based models without fitting parameters for pure metals, special subroutines for Ti, Mg, Ni-based superalloys, etc. Typical outputs are stress-strain curves for monotonic loading or fatigue life prediction (see Fig. 2).
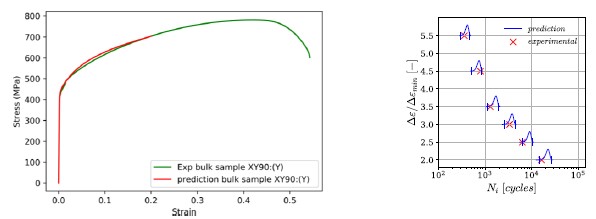
For more information, reach us at proyectos.materiales@imdea.org
[1] IMDEA Materials and Hexagon Partner for Next Gen Metal Simulation Tech. 3D print.com, 2020.