- Cada año se realizan más de cuatro millones de procedimientos de injertos óseos y reemplazo de huesos en todo el mundo. Se espera que este número aumente drásticamente en las próximas décadas debido al aumento de la esperanza de vida.
- Los investigadores de IMDEA Materiales están trabajando para acelerar el desarrollo de tratamientos térmicos de implantes en el proceso posterior a la fabricación, creando reemplazos óseos más duraderos, reduciendo las intervenciones quirúrgicas y mejorando la calidad de vida de los pacientes.
Los investigadores del Instituto IMDEA Materiales están trabajando para asegurar que los futuros implantes de reemplazo de huesos sean más duraderos y tengan una mayor vida útil.
La investigación, que se está llevando a cabo a través del proyecto M3TiAM financiado por la Unión Europea, está diseñada para satisfacer las necesidades de una población envejecida, ya que se espera que la demanda de procedimientos de reemplazo de huesos aumente en los próximos años.
El trabajo de IMDEA Materiales en el proyecto implica desarrollar herramientas computacionales innovadoras para predecir el efecto de los tratamientos térmicos posteriores a la fabricación en implantes novedosos de aleación de titanio (Ti) impresos en 3D.
En los últimos años, la fabricación aditiva (o impresión 3D) ha surgido como una de las tecnologías más prometedoras en la fabricación de implantes de reemplazo de huesos, ya que ofrece la capacidad de personalizar los implantes según las necesidades del paciente individual.
Esto ofrece varias ventajas, en particular al abordar lo que se conoce como apantallamiento de las tensiones (o stress shielding en inglés), un problema común causado por los tradicionales implantes óseos metálicos que resulta en tensiones cortantes entre el hueso y el implante.
Esto lleva a una reducción en la densidad, fuerza y rigidez de los huesos alrededor del implante, y una disminución consecuente en la salud y bienestar del paciente.
Los implantes impresos en 3D también pueden coincidir más precisamente con la geometría ósea y, además, mejorar el crecimiento óseo dentro de los implantes.
«Hoy en día, la idea de diseñar y fabricar implantes a través de la fabricación aditiva no es nada nueva, es una técnica de la que todos están tratando de emplear y sacar ventaja», explica el Dr. Adrián Boccardo.
Sin embargo, la novedad relativa de la tecnología (la primera cirugía exitosa de reemplazo de prótesis de cadera impresa en 3D se realizó en abril de este año) hace que los implantes impresos en 3D presenten algunas desventajas/limitaciones.
«Lo que hemos visto es que con la tecnología actual de impresión 3D, especialmente con la fusión selectiva por láser (SLM), las microestructuras de las piezas producidas son, en muchos casos, excesivamente frágiles», continúa el Dr. Boccardo.
«El material comúnmente sufrirá microdefectos que afectan al material a nivel atómico. Uno de los defectos más prevalentes es el alto nivel de microporosidad, que reduce la vida útil del implante.»
«Con el tiempo, estos defectos afectarán la funcionalidad de la pieza hasta el punto en el que necesite ser reemplazada quirúrgicamente, un procedimiento altamente invasivo que puede causar problemas de salud adicionales».
El Dr. Boccardo es el investigador principal del proyecto M3TiAM e Investigador Postdoctoral de las Acciones Marie-Skłodowska Curie. Es miembro del grupo de investigación de Modelado y Simulación de Procesado de Materiales del Instituto IMDEA Materiales, dirigido por el Dr. Damien Tourret.
Una de las vías más prometedoras para mitigar estos microdefectos, es a través de la implementación de tratamientos térmicos mejorados posterior a la impresión de los implantes.
Estos tratamientos permiten a los investigadores reajustar las aleaciones metálicas y se aplican comúnmente a piezas impresas en 3D para mejorar sus propiedades mecánicas, es decir, en el caso de M3TiAM, reduciendo la porosidad.
Los modelos computacionales para simular los efectos de las distintas opciones de tratamientos térmicos, que están siendo desarrollados por el Dr. Boccardo, conducirán a una reducción en la dependencia de costosos enfoques experimentales de prueba y error.
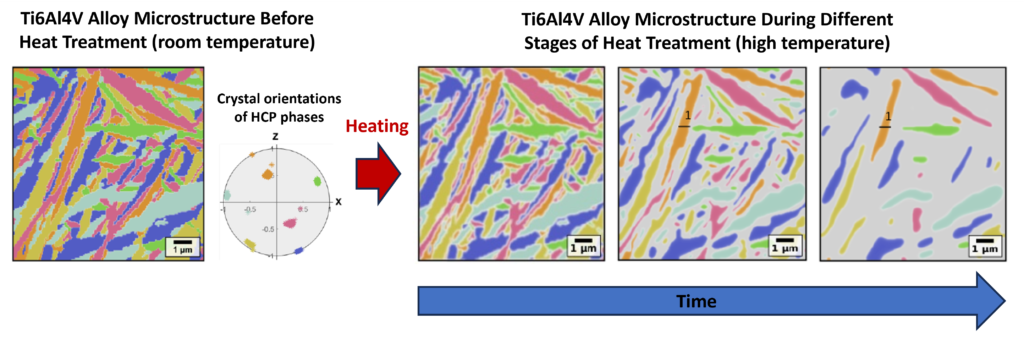
Esto, a su vez, dará como resultado a implantes que se diseñen y fabriquen más rápido, a menor costo, lo que finalmente los hará más asequibles y accesibles para los pacientes, algo de gran importancia para la industria de la salud dada la creciente demanda de implantes óseos, en particular los reemplazos de cadera y rodilla.
El aumento continuo de las expectativas de vida ha resultado en que los pacientes superen cada vez más la vida útil de sus implantes originales, lo que requiere una intervención quirúrgica secundaria para reemplazarlo.
Solo en Estados Unidos, se espera que para 2030 haya más de 635,000 reemplazos de cadera y 72,000 cirugías de revisión de cadera al año. La fractura ósea cerca del sitio del implante, el desgaste, la fatiga, la fractura y el aflojamiento del implante son factores que afectan negativamente la salud de los receptores de implantes.
De aquellos que se someten a un reemplazo de cadera, el 5% requerirá de una cirugía de revisión en un plazo de 10 años, aumentando al 15% en un plazo de 20 años, lo que representa potencialmente miles de intervenciones quirúrgicas evitables cada año.
En España, actualmente se colocan unas 35,000 prótesis de cadera anualmente.
Cualquier nuevo proceso de fabricación aditiva que surja del proyecto M3TiAM enfrentará un largo proceso de aprobación regulatoria y el típicamente complicado camino hacia la adopción industrial.
Sin embargo, el Dr. Boccardo se mantiene positivo de que los pacientes comenzarán a ver el impacto real de la tecnología de implantes mejorados en los próximos 5-10 años.
«Soy optimista porque las técnicas de fabricación aditiva con las que estamos trabajando ahora son bastante comunes», dijo. «Al mismo tiempo, las técnicas computacionales que estamos utilizando también son bastante estándar. Así que no estamos reinventando la rueda».
«El desafío aquí es combinar estas dos tecnologías ya establecidas de una manera que no se haya hecho antes y donde podamos lograr los mejores resultados».
El proyecto «Modelado Multiescala-Multifisico de Implantes Médicos de Aleación de Titanio basados en Tecnología de Fabricación Aditiva (M3TiAM)» ha recibido financiación del programa de investigación e innovación Horizon Europe de la Unión Europea bajo el acuerdo de subvención Marie Skłodowska-Curie No. 101063099. No obstante, los puntos de vista y opiniones expresados son exclusivamente los del autor o autores y no reflejan necesariamente los de la Unión Europea o la agencia ejecutiva de la Unión Europea. Ni la Unión Europea puede ser considerada responsable de los mismos.
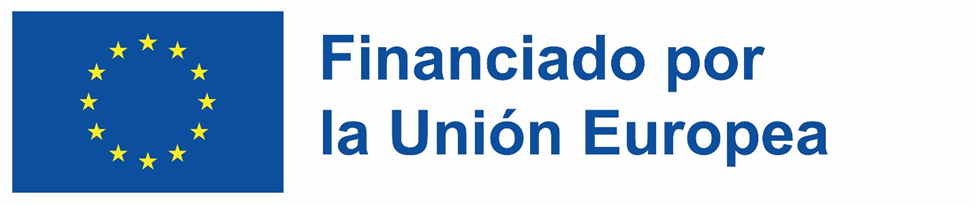