Funding:European Union, Clean Sky Joint Undertaking 2, Horizon 2020 Programme (Grant Agreement 821044)
Region: Europe
Project period: 2018 – 2021
Partners: CEIT-IK4 (Project Coordinator), IMDEA Materials Institute, Aubert & Duval SAS, Universidad del País Vasco, Interuniversitario Nazionale per la Scienza e Tecnologia dei Materiali (INSTM)
Principal Investigator at IMDEA: Dr. Ilchat Sabirov (ilchat.sabirov@imdea.org)
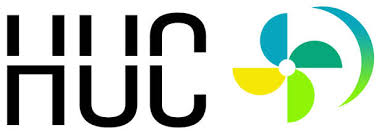
This project deals with the manufacture of IP Turbine casings for the new generation Ultrafan® engine from Astroloy using Net Shape Hot Isostatic Pressing of powder (NSHIP). Astroloy with high γ’ volume fraction have the required high temperature properties but it is unforgeable. Thus, Powder-HIP is the most promising process route for this alloy though this technique presents several challenges such as presence of PPBs in the HIPped microstructure, the high cost of powder and HIP-tooling. HUC, making usage of the background technology will face and overcome these challenges and will take a step further tackling technology gaps alongside the material capability, basic mechanical behaviour and impact in the presence of the exposure with the ultimate goal for this technology to be fully tested in the relevant UltraFan® Demonstrator engine environment.
The main objective of HUC is to improve the buy to fly ratio from the typically achieved 9 through the conventional cast and wrought route to less than 3 through NNSHIP being the material developed able to withstand engine relevant conditions with
and without exposure guaranteeing its ability to contain. The work plan includes the following main activities:
- Development and Optimisation of a powder HIP processing for Astroloy
- Characterisation of mechanical properties to generate a database which supports the component design
- Development of experiments and numerical simulations to assess the material´s behaviour under dynamic and ballistic
conditions - Characterisation and understanding of mechanical properties with exposure at high temperatures
- Development of low cost tooling for HIPping high temperature superalloy casings
- Development and validation of process modelling capabilities
- Manufacturing of canning/tooling to guarantee the compliance of the finish product with the requirements
- Project progress Management, Dissemination, Communication and Exploitation
Partners
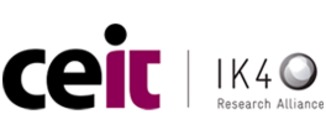
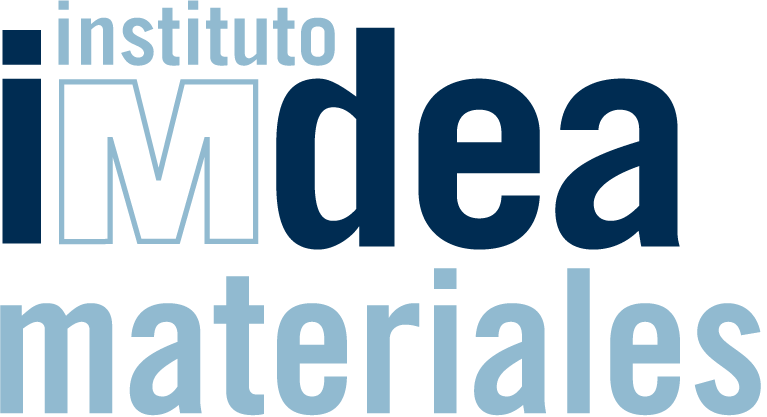
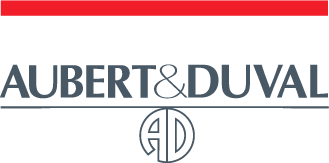
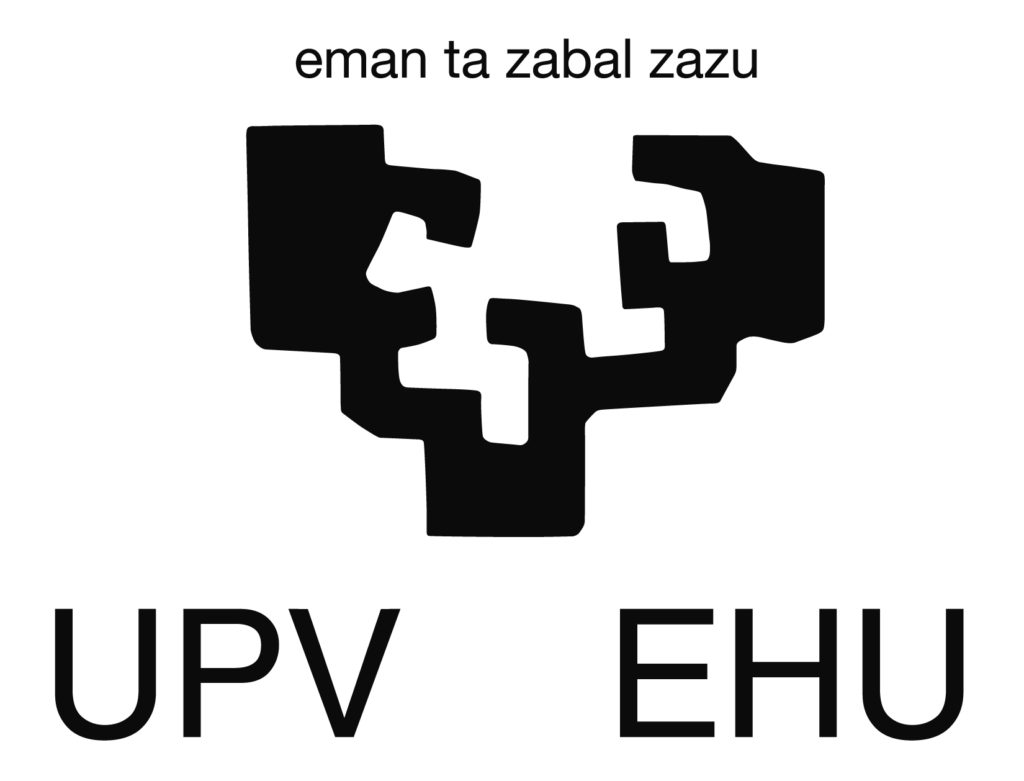
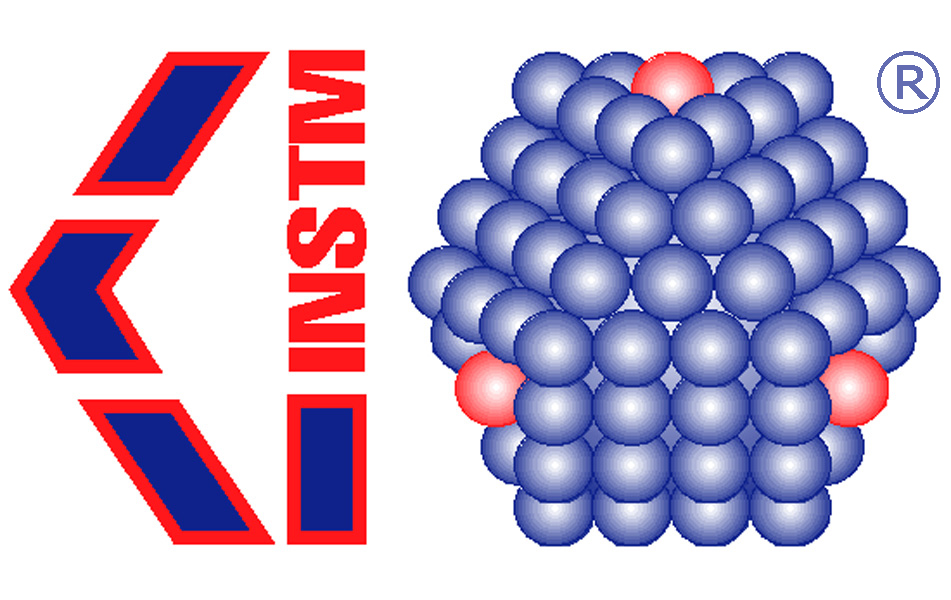
Funded by
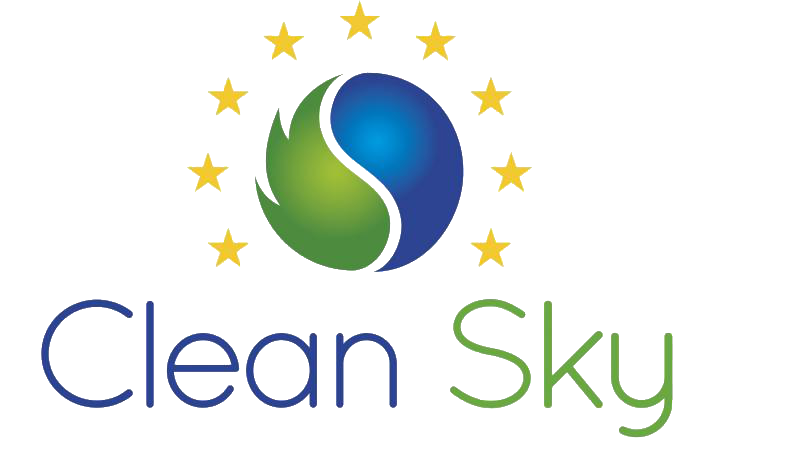
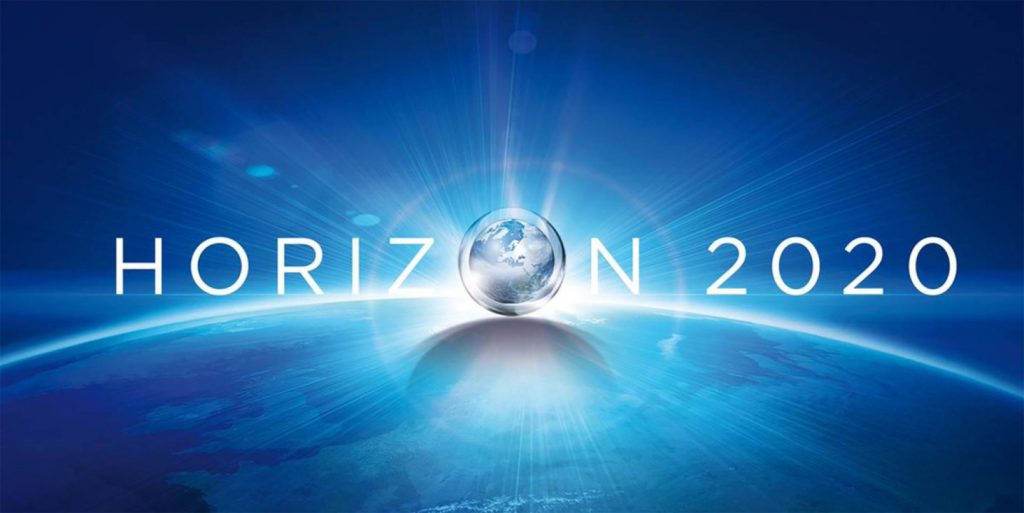